Exploring U.S. Steel Production: Facilities and Trends in 2024
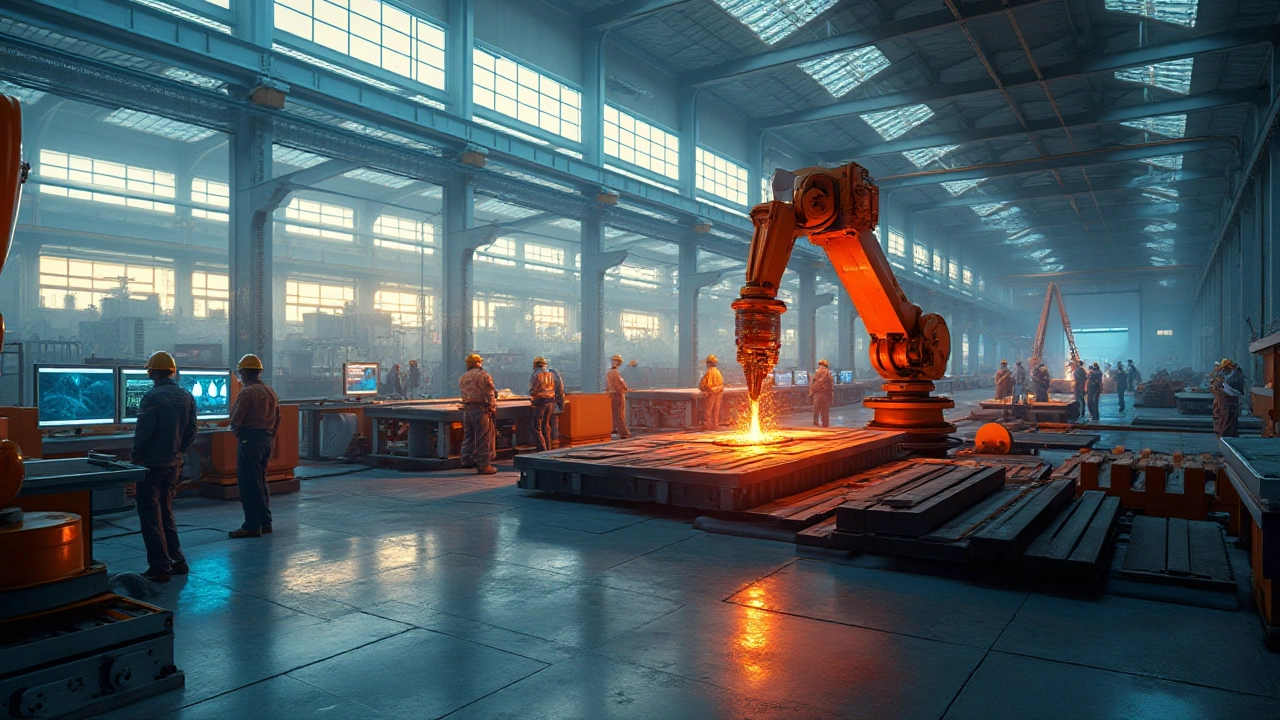
The United States, renowned for its vast and varied industrial capabilities, continues to play a significant role in steel production. Despite evolving challenges, from global competition to environmental concerns, America maintains an array of steel manufacturing plants that underscore its industrial might.
In exploring today's steel-making scene, we find stories of innovation woven with a rich history of craftsmanship. Key facilities across the country are not just keeping traditional methods alive but are also embracing cutting-edge technologies that redefine how steel is produced.
Amid these developments, policies and market trends shape the landscape, which demands a close look at the dynamics propelling the industry forward. We also must consider how an increasing demand for sustainable practices is influencing choices across this sector.
- The Current State of U.S. Steel Plants
- Technological Advancements in Steel Manufacturing
- Economic and Political Influences
- Sustainability in Steel Production
The Current State of U.S. Steel Plants
The landscape of U.S. steel production is dynamic and full of contrasts, reflecting the complexity of an industry in transition. Many of the leading steel plants are concentrated in the so-called 'Rust Belt' region, stretching across states like Ohio, Indiana, and Pennsylvania—but don't let the name fool you. These areas are thriving with innovation, as traditional industrial heartlands adapt to new realities. Nucor Corporation, the largest steel producer in the country, exemplifies how American steel manufacturing remains a force to be reckoned with. Employing electric arc furnaces known for reduced emissions, they are redefining what it means to produce steel sustainably while maintaining output at remarkable scales.
The technological advancements within the industry are reshaping facilities nationwide, from the coastal operations in Alabama's Mobile Bay to the inland hubs in Illinois. Each plant's story tells of adaptation and tenacity, like the recent modernization initiatives in the U.S. Steel's Gary Works, one of the largest integrated steel producers in North America. The plant's commitment to cutting-edge technologies, such as AI-powered process control, is leading to unprecedented levels of efficiency and quality.
U.S. steel plants are not just production sites but are embedded within the communities they serve, providing thousands of jobs and supporting local economies. For instance, the economic rebound in Youngstown, Ohio is closely tied to its thriving steel sector. Despite the industry's ups and downs, the unwavering spirit of resilience seen in these regions echoes across the broader spectrum of American manufacturing. These communities are buzzing with hope, driven largely by the resurgence in domestic demand and strategic investments aimed at boosting production capacity.
"The American steel industry remains a crucial backbone of the nation's economy," says Thomas Gibson, a long-standing authority in the field. "Our facilities are strategically positioned and continually advancing in technology, which allows us to meet and exceed market demands with agility."
Today, about seventy percent of steel in the U.S. is produced through mini-mills like those operated by Steel Dynamics, which offer increased flexibility and lesser environmental impact. The trend reflects a broader shift towards nimbleness and sustainability, both of which are essential in reducing the carbon footprint of steel plants USA. Despite the challenges, the U.S. continues to rank as a top steel producer globally, with an annual production of approximately 87 million metric tons as of recent counts. Industry leaders remain bullish about future growth, buoyed by factors including government infrastructure projects and a renewed emphasis on strengthening domestic supply chains.
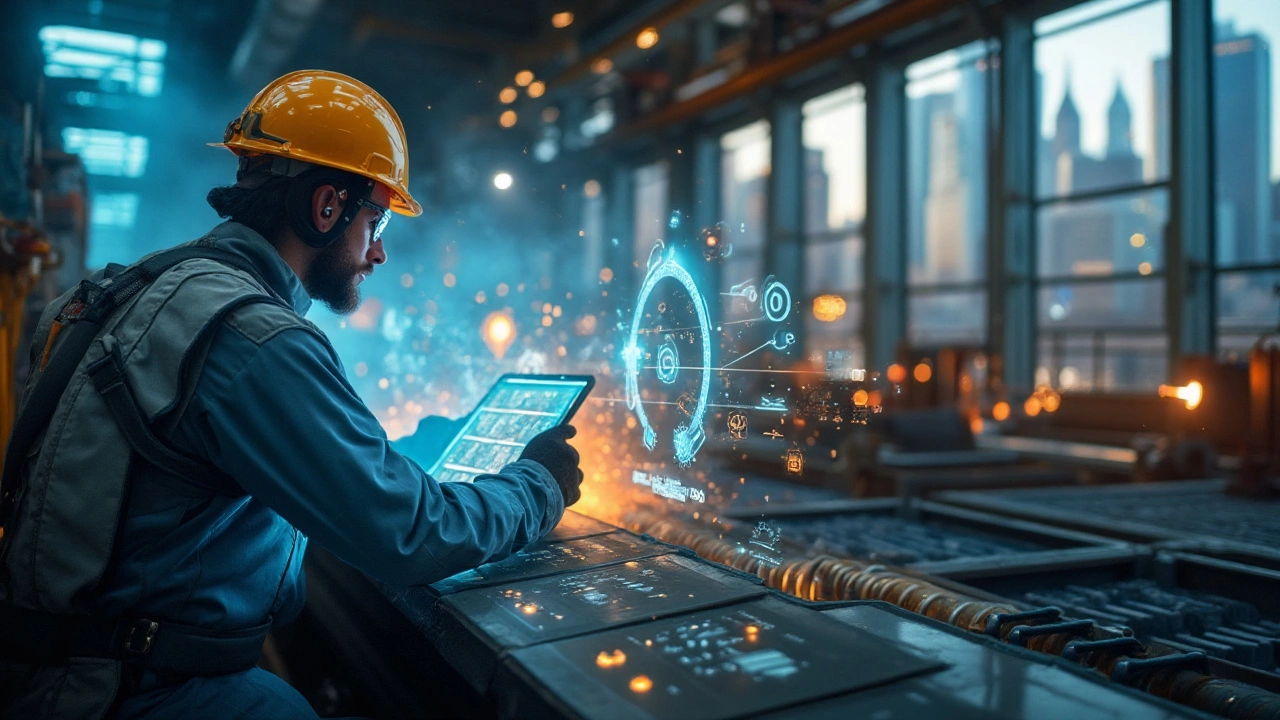
Technological Advancements in Steel Manufacturing
The steel industry in the United States is witnessing a transformative phase driven by a wave of technological advancements. As of 2024, steel plants across the nation are leveraging cutting-edge technology to optimize production processes, improve energy efficiency, and enhance product quality. These advancements are pivotal in maintaining the competitiveness of U.S. steel production in a globally competitive market.
One of the most significant innovations revolutionizing the industry is the integration of automation and IoT (Internet of Things). Various plants have adopted smart sensors and real-time data analytics to monitor and control production with unprecedented precision. These technologies not only reduce downtime and maintenance costs but also enhance the safety and working conditions for plant employees. A push towards digital transformation through AI-driven systems is reshaping the steel manufacturing landscape, enabling plants to predict and troubleshoot operational issues before they snowball into disruptions.
Another leap forward is found in the development of advanced materials and metallurgical techniques. Steel manufacturers are constantly researching to improve the strength-to-weight ratio of their products. High-strength, low-alloy (HSLA) steels are becoming increasingly popular, especially in the automotive and construction sectors where durability coupled with lightness is critical. Research into nanotechnology is also being closely watched, as nanostructured materials promise even more formidable capabilities and longevity.
3D printing, or additive manufacturing, is yet another frontier that offers exciting possibilities for steel components. By allowing intricate designs that traditional methods struggle to achieve, 3D printing offers cost-effectiveness and efficiency advantages by reducing waste material and production time. While this technology is still maturing, its potential applications across various industries, from aerospace to biomedical, are immense.
"The future of steel manufacturing lies in the symbiotic relationship between traditional expertise and digital innovation," as observed by a leading industry expert during a recent conference.
The quest for sustainability is also driving technological progress in steel making. The industry is increasingly focusing on reducing carbon footprints, given the rising concerns around climate change. Steel plants are investing in cleaner energy sources, like hydrogen fuel and electric arc furnaces, significantly curbing CO2 emissions. Additionally, there is an ongoing trend of utilizing waste products in innovative ways, turning by-products into assets rather than liabilities.
Data shows that energy efficiency measures have led to significant energy savings, with some facilities achieving nearly a 30% reduction in energy use. This underscores the strategic shift towards more sustainable methods, balancing between economic viability and environmental responsibility. Highlighting these advancements demonstrates how the U.S. steel sector not only meets current demands but also aligns with future objectives, establishing a resilient foundation for growth.
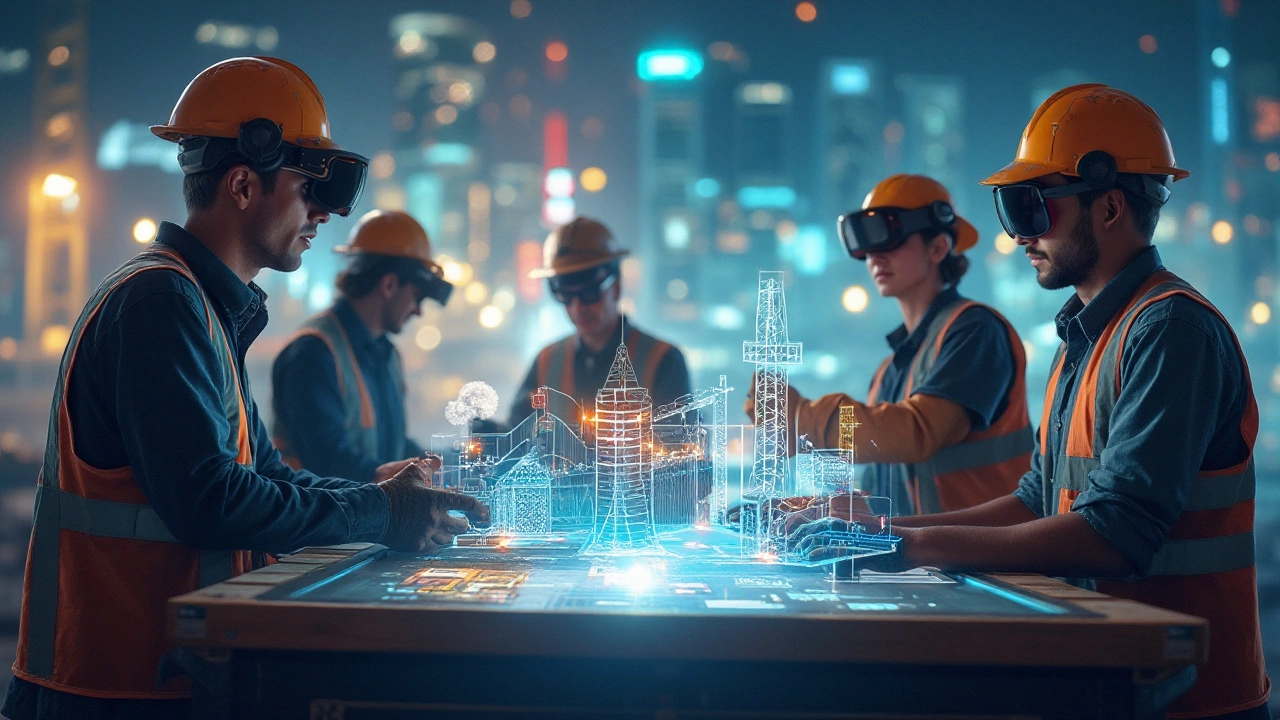
Economic and Political Influences
The landscape of the steel industry in the United States is profoundly shaped by a tapestry of economic and political influences. Various administrations have historically wielded significant power over this sector through their policies, impacting everything from trade tariffs to environmental regulations. At times, government interventions have been pivotal in protecting the domestic market against international competitors, particularly with strategies aimed at addressing unfair trade practices. For instance, tariffs imposed on imported steel often play a critical role in leveling the playing field for local manufacturers, allowing them to sustain operations and invest in innovation.
In current times, economic policies continue to steer the direction of U.S. steel production. Tax incentives for industries adopting cleaner technologies have encouraged companies to invest in environmentally friendly practices. This shift not only enhances sustainability but also boosts competitiveness on the global stage. Additionally, the thriving construction industry has consistently driven demand for steel, supported by government investments in infrastructure projects aimed at modernizing the nation's foundations. This synergy between policy and market demand prompts a cycle of reinforcement beneficial to the nation’s economic health.
Political decisions, however, can also introduce complexities. International relations often influence trade agreements or disputes that affect the cost and availability of raw materials, which are crucial for American manufacturing. Efforts to negotiate trade deals while maintaining protective measures for domestic industries require a delicate balance. As a senior executive at a leading steel plant commented,
"Navigating through the labyrinth of government policies and international trade terms remains as challenging as forging the steel itself, yet it's an art we must continually refine."
The geopolitical climate further introduces elements of unpredictability. Sudden shifts in political alliances or global events can cause ripples that impact supply chains, labor dynamics, and capital flows. This has led many industry leaders to adopt more resilient and flexible business models, ensuring stability amidst uncertainties. Recognizing this, industry analysts highlight the importance of fostering strong relationships with governmental bodies to align industry goals with public policies effectively.
Also worth noting is the pivotal role of lobbying within the steel industry. Significant resources are often allocated to influence legislation that favors the domestic steel plants USA operates. These efforts help mitigate risks imposed by unfavorable policies and ensure a conducive environment for growth and advancement. With the ever-evolving landscape, industry players must remain agile, navigating the intricacies of political and economic pressures while capitalizing on opportunities that arise.
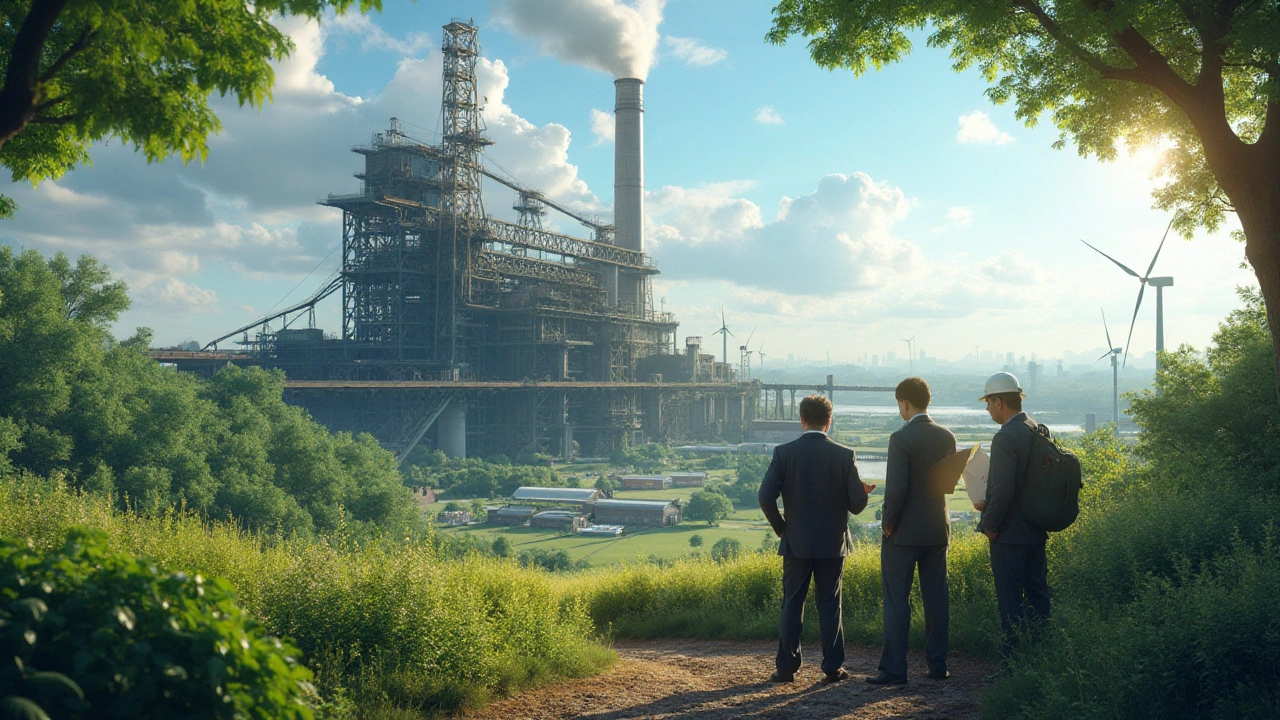
Sustainability in Steel Production
As climate concerns reverberate globally, the U.S. steel production industry is on a path seeking greener pastures. This is not just a trend but an essential transition. Traditional steel manufacturing is notoriously energy-intensive and a significant contributor to carbon emissions. However, American steelmakers are harnessing innovation to craft a future where sustainability gradually becomes the norm. From adopting electric arc furnaces, which rely on recycled scrap steel and consume considerably less energy, to the introduction of carbon capture technologies, they are reimagining the way steel is produced, with a significantly lower carbon footprint.
One of the most exciting developments has been the increased focus on using hydrogen as a reductant in place of coal. This shift holds potential promise, as hydrogen-based steelmaking, still in its nascent stages, can dramatically reduce emissions compared to conventional methods. The challenge lies in scaling such technologies effectively and cost-efficiently. Industry leaders like ArcelorMittal and Nucor are already investing heavily in research and collaborations to bring these sustainable practices to life. Such measures ensure that the industry not only meets regulatory requirements but also paves the way for future generations.
"The steel industry can lead the charge on industrial decarbonization," says Dr. Samantha Chapman, a leading energy economist. "By investing in clean technologies today, we secure not just the planet, but also a competitive edge for tomorrow's markets."
In addition to technological innovation, there is a growing narrative around the circular economy within steel production. The concept revolves around reducing waste and continually recycling materials to keep them within the production loop. The American Iron and Steel Institute reports that steel is the most recycled material in North America, boasting a substantial recycling rate of over 88%. Such statistics underscore the untapped potential for recycled steel to significantly lessen the industry's environmental impact while supporting sustainable growth.
Economic and political influences also play a significant role. Government mandates and policies aimed at combating climate change are setting new standards and driving the industry to innovate. Tax incentives and subsidies for sustainable initiatives are helping ease the transition for manufacturers aiming to revamp their practices. International steel trade agreements may also include components that emphasize environmental responsibility, encouraging global adherence to green standards.
As we look towards the future, the dual focus on innovation and eco-conscious practices suggests that sustainable steel production will become not just a possibility but a mainstream reality in the coming decades. It's a narrative weaving through boardrooms and policy discussions as both a moral imperative and market opportunity. By stepping up to the challenge, the U.S. steel sector is not only safeguarding its future but also contributing to a broader, global effort to protect the environment.