The Factory System: A Game-Changer for Economics
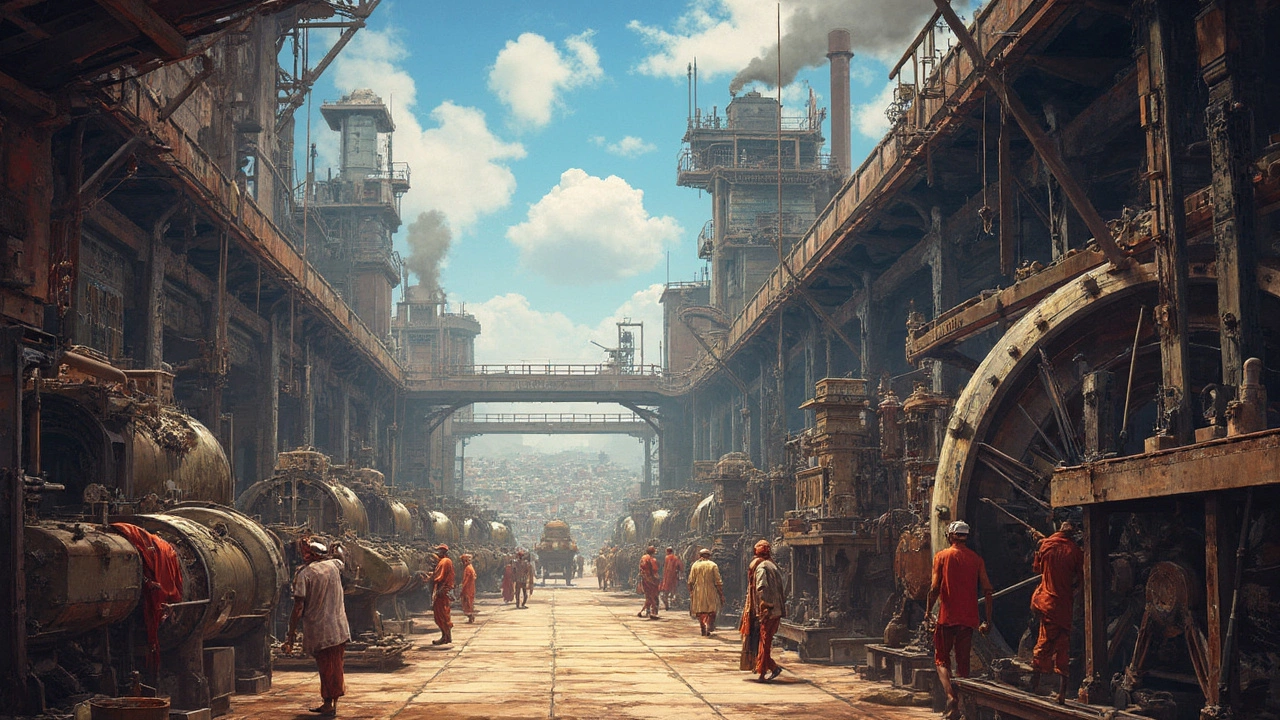
Ever wonder how the factory system turned the world of manufacturing on its head? It's a big part of how we got to where we are now, economically speaking. Basically, bringing everything under one roof - the whole shebang from raw material processing to finishing products - was a game-changer. Before this, people were crafting things in their homes or tiny workshops. With the factory system, it became possible to produce stuff on a massive scale.
The benefit? Well, one major perk is cost efficiency. Imagine this: instead of making one shirt a day, factories started churning out hundreds. More bang for your buck, right? This kind of efficiency drove production costs down, and products became way more affordable. Think of your favorite gadgets today - they wouldn't be in every household without this shift.
- The Birth of the Factory System
- Revolutionizing Production
- Cutting Costs and Boosting Efficiency
- Impact on Employment and Society
- The Role of Government Schemes
- Modern Implications and Future Trends
The Birth of the Factory System
Picture this: it's the late 18th century, and the world is dipping its toes into the waters of the Industrial Revolution. This is when the factory system really started taking off. Before this, most goods were crafted by hand in small workshops or homes, known as the cottage industry. This method was slow and limited, ensuring that only the wealthy could afford many products.
But things were about to change. Enterprising folks like Richard Arkwright and Samuel Slater were instrumental in creating the first factories. Arkwright, for instance, is often credited with inventing the water frame in 1769, which used water power to spin cotton into yarn. His success laid the groundwork for the modern factory system. By centralizing production processes, he created a model that could be replicated across industries.
The Role of Technology
This transformation wouldn't have been possible without technological advancements. Machines like the spinning jenny and the power loom revolutionized the textile industry, which was really the starting point for the factory system. These machines increased output at a pace that was unheard of before.
Mass production started to redefine the economic landscape. Suddenly, it wasn't just about producing more - it was also about doing it cheaper and faster than ever. This fed into urbanization, as workers moved toward these industrial hubs, seeking employment in the new factories.
Government Schemes to Support Growth
A big part of this shift was how governments got involved. They started recognizing that supporting these factories meant boosting their economies. Infrastructure projects like building railroads and canals became crucial as they facilitated the transport of raw materials and finished goods. Plus, laws and policies that encouraged innovation and protected nascent industries started cropping up.
This was just the beginning of a journey that would see the world move from handmade goods to the automated, mass-produced products we know today. It was a turning point that not only changed how things were made but also who could buy them and how economies thrived.
Revolutionizing Production
The factory system didn't just tweak production methods; it completely overhauled them. Before industrialization hit full steam, manufacturing was pretty much a cottage industry. But when factories started crop up, everything about production changed.
Centralized Production
The idea of having all production stages under one roof was groundbreaking. This centralization meant materials could move quickly through a streamlined process. Imagine, instead of wasting time shipping parts from place to place, they just rolled down the line. Simple but genius, right?
Specialization of Labor
Once factories became a thing, workers could specialize in specific tasks. No more jack-of-all-trades stuff. By focusing on one part of the process, workers became incredibly skilled and efficient. It's like how in today’s production lines, one person might screw on caps while another fits labels. Together, they get more done without the confusion.
Impact on Speed and Scale
With everything centralized and a specialized workforce, the scale and speed of production skyrocketed. Say you were making shoes; instead of producing a handful a week in a workshop, factories could now produce hundreds or even thousands in the same time. That’s a massive leap, making goods way cheaper and more available.
Innovation and Adaptability
The leap didn’t stop there. The factory system encouraged innovation, leading to more efficient machines and processes. Adapting to new tech became crucial, which meant factories often led the market in adopting the latest advancements.
Manufacturing and how it transformed during the industrial revolution set the stage for modern production. And who knows? Maybe the next great shift is already brewing out there, just like it was back then.
Cutting Costs and Boosting Efficiency
The shift to the factory system was a huge deal in terms of cost and efficiency. Imagine a time when each item was handcrafted, leading to a lot of time and effort for just a single product. With factories, everything changed. By centralizing production, manufacturers slashed costs, which meant they could offer products at a cheaper price. This wasn't just good for the businesses; it was game-changing for consumers too.
The magic really happened with the division of labor. Instead of one worker doing multiple tasks, each worker focused on one specific job. This specialization didn't only cut down training time; it made workers faster and better at what they did. Think of it like an assembly line where every part has a purpose, from screwing in bolts to final inspections. It's like the difference between hand-painting a picture and running it through a printer – speed and precision.
The Role of Technology
Another big piece of the puzzle was the use of machinery. Early factories started using steam engines to power machines, which replaced manual labor. This meant hundreds of products could be made way quicker. Technology stepped up productivity and sliced down production times massively. Just look at the textile industry – powered looms were weaving cloth much faster than any skilled hand-weaver could.
- Mass Production: The ability to create large quantities of goods in a short time was revolutionary. More goods meant more sales, which meant more money pumping through local economies.
- Standardization: Producing large quantities helped in setting consistent quality standards. Products became more reliable, building greater consumer trust.
Economic Impact
This wasn't just about making factory owners richer. Lower costs of production filtered down to lower consumer prices, so everyday folks could suddenly afford things only the wealthy had before. More people buying products also meant a larger economic cycle, pushing more money into development and innovation.
If we peek at some data, a basic textile worker saw their output per hour triple in efficiency from pre-industrial times to the mid-1800s thanks to the factory system. Talk about a productivity boom!
Year | Output per Worker |
---|---|
1750 | 50 units |
1850 | 150 units |
These improvements laid the groundwork for modern manufacturing. While the scale and tech have only grown, the fundamentals of cost-cutting and efficiency through the factory system remain the bedrock of manufacturing today.
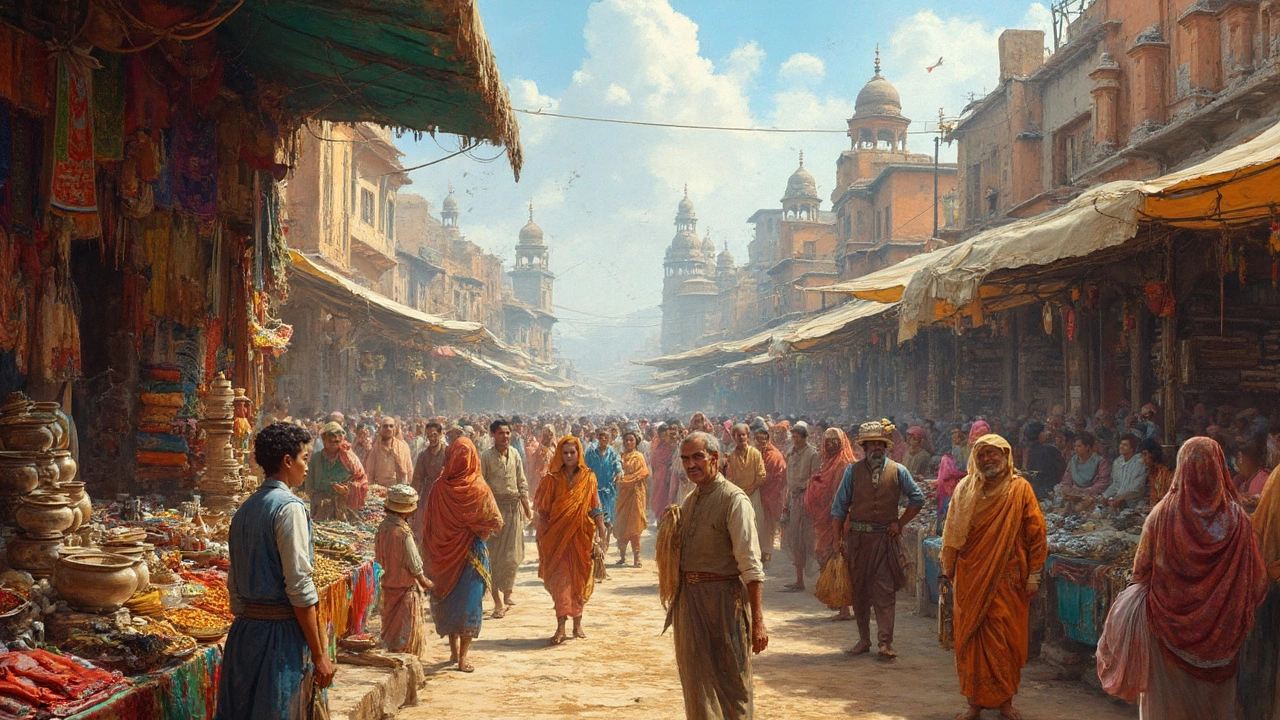
Impact on Employment and Society
The rise of the factory system didn’t just change how stuff was made. It totally transformed lives, starting with job availability. Before factories became a thing, most folks were working in agriculture or doing small-scale crafting jobs. When factories popped up, tons of new jobs were created. Suddenly, people flocked to cities looking for work, and bam! Urbanization kicked off.
This shift to manufacturing jobs wasn't without its challenges, though. Back in the day, working conditions weren’t exactly a bed of roses. Long hours, dangerous machinery, and low pay were common concerns. But over time, efforts to improve these conditions led to labor laws and unions that fought for better rights.
This change also stirred up societal shifts. Think of it this way: with more reliable incomes, families could afford better living standards. Over generations, this contributed to improved education and eventually led to advancements in health and social services. It set the stage for modern amenities we often take for granted today.
Change in Social Structure
The ripple effect of the factory system wasn’t just about jobs. Whole communities were shaped by it. For example, some cities that were previously just dots on the map became bustling hubs thanks to factories. This growth necessitated more houses, schools, and shops—basically a whole new way of living.
Government's Role
Yep, government schemes had a big hand here too. Incentives were often given to establish factories or improve existing setups. In the UK, during the Industrial Revolution, these schemes helped craft policies that encouraged factory-based production. Over time, this collaboration between public and private sectors helped stabilize economic growth and job security.
Period | Urban Population Growth |
---|---|
Early 1800s | 17% |
Late 1800s | 54% |
1930s | 68% |
Ultimately, the impact of the factory system on employment and society was profound, driving changes still felt today. It marked the start of a journey that linked economic practices with cultural and social development, creating echoes across history.
The Role of Government Schemes
Let's talk about how government schemes played a huge role in the factory system taking off. Without some solid support from the government, we might not have seen factories pop up everywhere as they did.
Back in the day, governments figured out that investing in manufacturing could really ramp up the economy. They started offering incentives to encourage the establishment of factories. Things like tax breaks, subsidies, and even direct funding to set up infrastructure were pretty common. By sweetening the deal, they wanted more folks to dive into the factory business.
Infrastructure Development
Building up the nation’s infrastructure was crucial. Roads, railways, and ports were developed to smooth logistics and cut down transport costs. This meant manufacturing hubs could distribute products quickly and cheaply, which was a win-win for businesses and consumers.
Workforce Training Programs
But there was more to it than just roads and rails. Governments also started workforce training programs to ensure there were skilled workers ready to fill all those new jobs. Apprenticeship schemes and vocational institutes became a norm. After all, someone needed to know how to run the machines and keep everything moving smoothly.
Case in Point: The Industrial Revolution
A classic example is Great Britain during the Industrial Revolution. The government’s support in terms of improved patent laws and capital availability made it a breeding ground for industrial growth. Entrepreneurs found it easier to innovate and protect their inventions, promoting a safer environment for investment.
Scheme | Country | Benefit |
---|---|---|
Tax Breaks | USA | Lowered financial barriers for starting new factories |
Subsidized Loans | UK | Encouraged expansion and modernization of factories |
All these moves weren't just about getting factories up and running. They were about molding a well-oiled economy, boosting employment, and making consumer goods affordable to more people. The factory system, backed by government schemes, reshaped not just industries but entire societies. It's wild how this mix of policy and production shaped the world we live in today!
Modern Implications and Future Trends
So, what does the factory system mean for us today and tomorrow? The truth is, it’s still massively shaping the landscape of production and our economy.
Technological Integration
Manufacturing now means integrating smart tech and automation. We’re talking robots working alongside people, optimizing production time, cutting down errors, and keeping the costs even lower. Factories are getting smarter with tech like AI guiding processes, predicting maintenance needs before something breaks down. Imagine the savings in downtime alone!
Sustainability in Focus
Then there’s the biggie—sustainability. Today’s consumers and governments demand greener solutions. Factories are adapting by using renewable energy sources, recycling materials, and cutting waste. It’s not just about cost; it’s about responsibility.
Global Supply Chains
With globalization, factories aren’t just about local production anymore. Products often cross borders multiple times before reaching us. This global supply network makes efficiency and reliability crucial, especially when disruptions hit like during a pandemic. Factory systems play a vital role in smoothing out these hiccups.
The Human Element
Let’s not forget about the workforce. While automation is taking over certain roles, there’s a growing need for skilled jobs to manage these systems—techies, engineers, and problem-solvers. Upskilling programs and government initiatives are popping up to fill these gaps, ensuring workers aren't left behind.
Trend | Impact |
---|---|
Automation | Increased efficiency and reduced costs |
Sustainability | Less environmental impact and compliance with regulations |
Globalization | Broader market reach and diverse supply chains |
Upskilling | Creation of tech-savvy jobs and economic stability |
In essence, the factory system is adapting, evolving with the times, yet still sticking to its roots of making production more efficient. As we look to the future, it’s about balance—embracing technology while ensuring sustainability and economic growth.