Where Is Plastic Made in the USA?
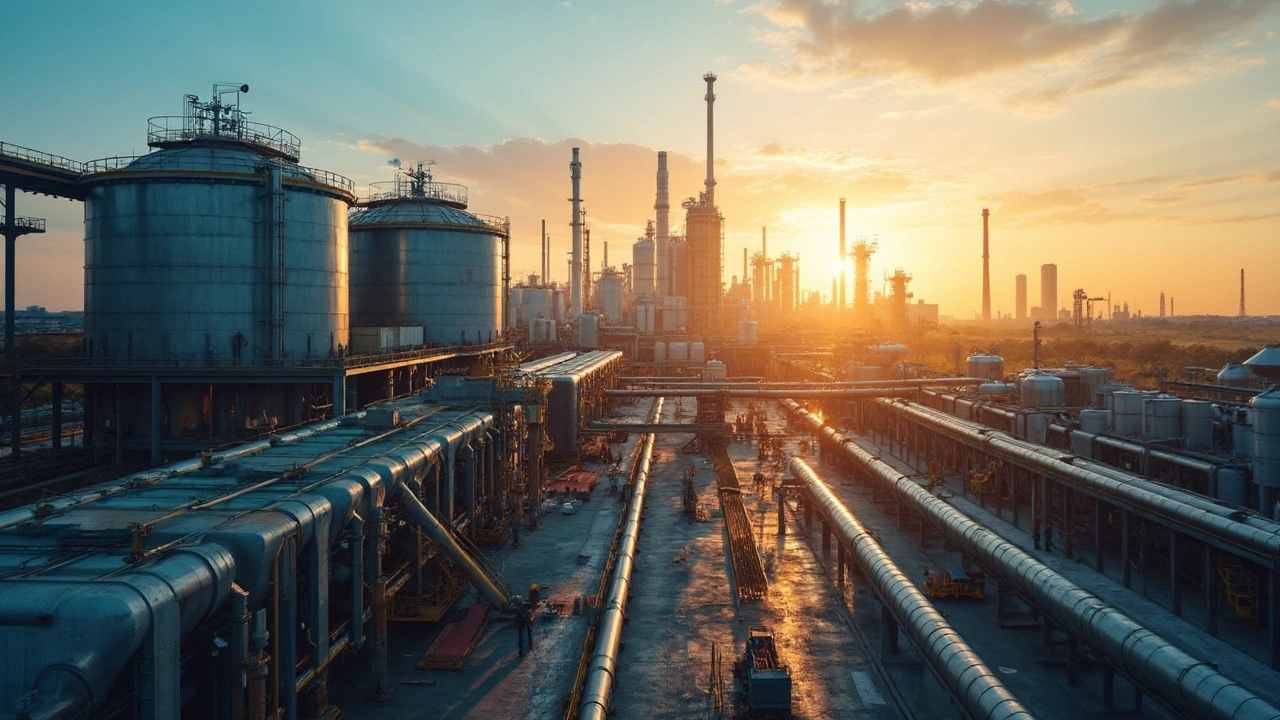
When you think about where all the plastic comes from, the USA has got some serious contenders in this space. Certain states are practically plastic manufacturing hotspots, thanks to nearby oil refineries and established infrastructures. Texas, for example, is a major player due to its vast oil resources and skilled workforce. It's not just about the oil though—it's also about having the know-how and facilities to turn raw materials into something useful.
Ohio is another key state, leveraging its central location and industrial history to boost its plastic production. The state has a mix of older, established companies and newer entities bringing fresh technology to the table. This blend keeps the industry innovative and competitive while supplying materials to countless markets.
- Key Plastic Manufacturing Regions
- Big Players in the Industry
- How Plastic Is Made
- Environmental Considerations
- Future Trends in Plastic Manufacturing
Key Plastic Manufacturing Regions
Plastic manufacturing takes place all over the USA, but certain areas really stand out because of their strategic advantages. Texas, for instance, ranks among the top due to its wealth of natural resources. It's not just about having oil; it's about having the refineries, infrastructure, and workforce to turn that oil into plastic. The Gulf Coast is littered with chemical plants, making this region an industrial powerhouse.
Texas - The Powerhouse
If you've ever driven along the Gulf Coast, you've undoubtedly noticed the sprawling refineries. They play a crucial role in the plastic manufacturing landscape, with big names like ExxonMobil and LyondellBasell operating in the area. Texas' infrastructure, like major ports and transportation networks, facilitates a smooth supply chain, making it a kingpin in the industry.
Ohio - The Central Hub
Ohio might not have the oil fields of Texas, but it makes up for that with its strategic central location. Situated near the Great Lakes and several major highways, it serves as a convenient distribution point. Companies like Berry Global and PolyOne have a presence here. The state's long manufacturing history means there's a skilled labor pool ready to produce high-quality plastic products.
Interesting Facts About Plastic Production
Here's a quick glance at where some plastic companies have made their home:
- California is home to innovative companies focusing on biodegradable plastics.
- Pennsylvania has a vibrant industry thanks to its proximity to Marcellus Shale natural gas.
- Louisiana, much like Texas, benefits from its Gulf Coast location, packed with chemical plants.
Why Location Matters
The placement of manufacturing plants isn't random. Proximity to raw materials, skilled labor, and infrastructure are key factors. Being close to raw material sources, like oil and natural gas fields, lowers costs and increases efficiency. Similarly, access to ports and highways ensures products get to market smoothly and quickly.
Understanding these regions helps you see why the USA stays competitive in the plastic manufacturing market. Each area brings something unique to the table, ensuring a varied and robust industry that keeps the modern world moving.
Big Players in the Industry
Alright, let's talk about who’s leading the charge when it comes to plastic manufacturing in the USA. It’s not just a handful of companies—some major players dominate the scene.
Chemical Giants
First up, we have Dow Inc., headquartered in Midland, Michigan. They’re one of the largest chemical manufacturers in the world, and their portfolio covers everything from plastics to specialty materials. Pretty much anything you can think of that involves polymers, Dow has a hand in making it.
Next on the list is ExxonMobil Chemical, based in Texas. They use their extensive oil and gas resources to produce a wide range of plastics. It’s not just about their production capacity; it’s their integrated supply chain that makes them a beast in the industry.
Versatile Manufacturers
LyondellBasell, also with operations in Texas, deserves a shoutout. Renowned for their innovative approaches, they focus on producing both basic and advanced plastics. Their products are used in automotive parts, packaging, and so much more.
Then we have Eastman Chemical Company from Kingsport, Tennessee. They specialize in specialty plastics, catering to industries requiring highly customized solutions, such as electronics and healthcare.
Manufacturers Thriving on Innovation
Let’s not forget DuPont, based in Delaware. Known for their innovative breakthroughs, they constantly evolve with market demands, producing everything from lightweight plastics for vehicles to durable materials for construction.
Company | Headquarters | Main Products |
---|---|---|
Dow Inc. | Midland, MI | Plastics, specialty materials |
ExxonMobil Chemical | Texas | Basic and advanced plastics |
LyondellBasell | Texas | Automotive, packaging plastics |
Eastman Chemical Co. | Kingsport, TN | Specialty plastics |
DuPont | Delaware | Innovation-driven plastics |
These companies are not only leading in plastic manufacturing but are also influencing market trends and tackling sustainability challenges. They’re pushing the boundaries in creating everyday products and exploring the future of the industry.
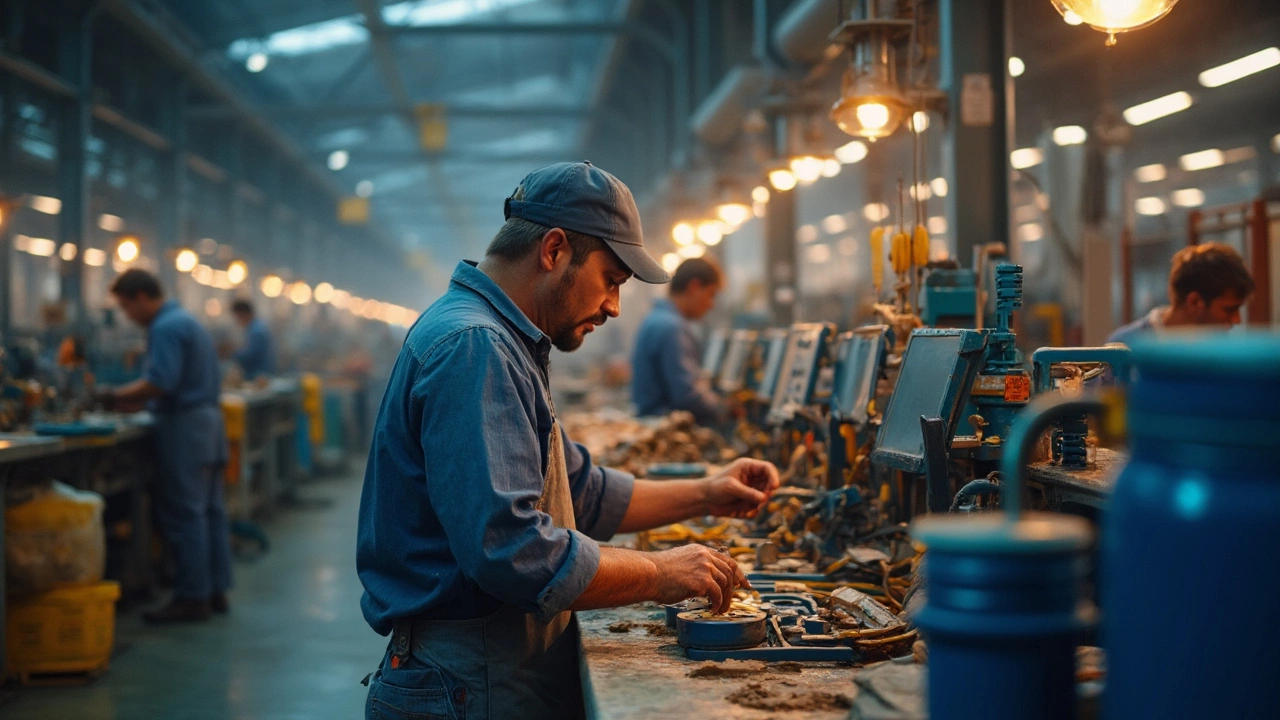
How Plastic Is Made
Have you ever wondered how plastic moves from being a raw material to the stuff wrapped around your sandwich? It's a cool process! To understand this, let’s break it down step by step.
1. Raw Material Extraction
The journey begins with raw materials. Most plastic starts as a fossil fuel product like natural gas or crude oil. In the USA, places with strong oil industries, like Texas, are crucial for this step.
2. Polymerization
Next, it's all about chemistry. The raw materials go through a process called polymerization. In simple terms, they’re heated and combined to form long chains of molecules known as polymers. These polymers are the base for different types of plastic used in various products.
3. Compounding
Polymer chains on their own won't do much. During compounding, additives like colors, fillers, and stabilizers get blended in. This mixture is made into small pellets, which are easier to handle during manufacturing.
4. Manufacturing
The plastic pellets are sent to manufacturing facilities spread across the USA, including states like Ohio. There, they’re melted and molded into various shapes through methods like injection molding or extrusion. This transformation turns the pellets into finished products or components used in multiple industries.
5. Distribution
Finally, the products are shipped out to distributors or directly to businesses needing these plastic components. The USA's vast transportation network plays a key role here, ensuring products reach the national and even global market efficiently.
Understanding these steps can give you a glimpse into just how sophisticated the plastic manufacturing process really is. It's a fascinating blend of science and industry, delivering materials that touch almost every aspect of our daily lives.
Environmental Considerations
Let's face it, the environmental impact of plastic manufacturing is a big topic. With the plastic manufacturing industry being so vast in the USA, it naturally brings along some environmental baggage. One key area of concern is the high energy consumption needed for production, coupled with significant greenhouse gas emissions. According to the Center for International Environmental Law, "The production and incineration of plastic will add 850 million metric tons of greenhouse gases to the atmosphere in 2019."
Another issue is waste. The plastic industry's footprint on landfills can’t be ignored. Despite strides in recycling, a significant chunk of used plastic still ends up in the garbage. Addressing this involves boosting recycling rates and finding innovative ways to repurpose plastic waste.
Recycling and Innovations
Thankfully, there are ongoing efforts to improve how plastic is recycled. Companies are investing in advanced sorting technologies to increase the efficiency of separating plastics for recycling. Some innovations involve converting plastic waste into fuel or other valuable resources.
States like California are leading by example, implementing stricter regulations and pushing for a more sustainable approach industry-wide. And with more companies joining the bandwagon, the future could see a substantial reduction in plastic's environmental footprint.
Future Outlook
In the coming years, the focus on green manufacturing is expected to ramp up. There's talk of using bioplastics, which are made from renewable sources and decompose faster. Partnerships between big industry players and environmental groups could foster new breakthroughs in eco-friendly production methods.
Year | Projected Plastic Waste |
---|---|
2025 | 275 million tons |
2030 | 350 million tons |
While challenges remain, the momentum towards a greener industry is building. In the world of plastic manufacturing, change is not only good, it's necessary.
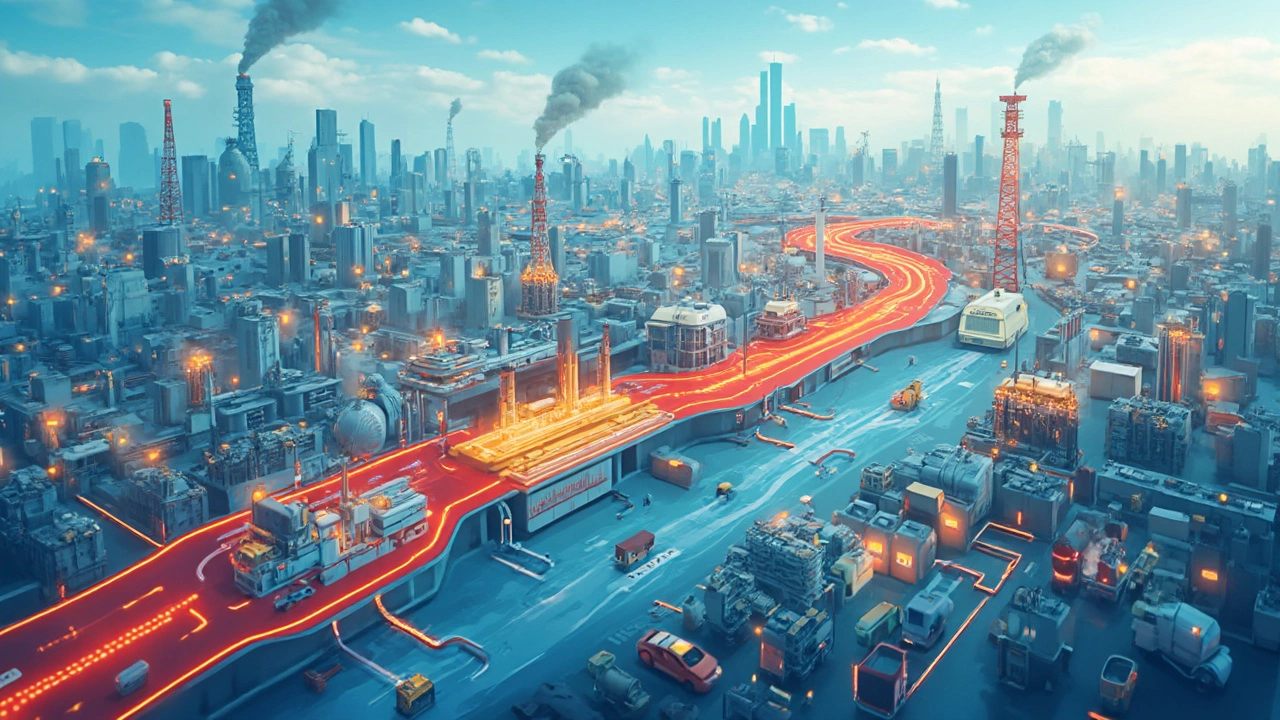
Future Trends in Plastic Manufacturing
Plastic manufacturing is not staying put; it's heading into a future packed with innovation and responsibility. One of the biggest shifts is toward sustainable practices. Companies are increasingly using bioplastics, derived from renewable sources like corn starch and sugarcane, instead of traditional petroleum-based materials. These bioplastics help reduce the carbon footprint and are a step towards a greener future.
Embracing Recycling Technologies
Recycling is getting a major facelift with advanced technologies. Chemical recycling is becoming more common as it breaks down plastics into their original building blocks, allowing for more versatile use. This approach generates less waste compared to traditional methods and is gaining traction in the industry.
Automation and Digital Integration
The leap into automation is significant. Robotics and AI are being integrated into manufacturing processes to boost efficiency and reduce human error. This trend is especially strong at large facilities in Texas and Ohio, where they can optimize production lines and reduce costs.
3D Printing Revolution
3D printing is transforming how products are designed and produced. Using plastics in 3D printing offers flexibility and customization like never before. It's opening up new possibilities for on-demand manufacturing, which can significantly cut down on waste and costs.
Policy Changes and Industry Regulations
Lastly, industry regulations are tightening to tackle plastic pollution. Policies focusing on single-use plastics are encouraging companies to explore alternative materials and incorporate *plastic manufacturing* practices that are environmentally friendly. This regulatory landscape is crucial in steering the industry towards innovation that aligns with environmental goals.