Why the Manufacturing Industry is Struggling: Examining Government Interventions
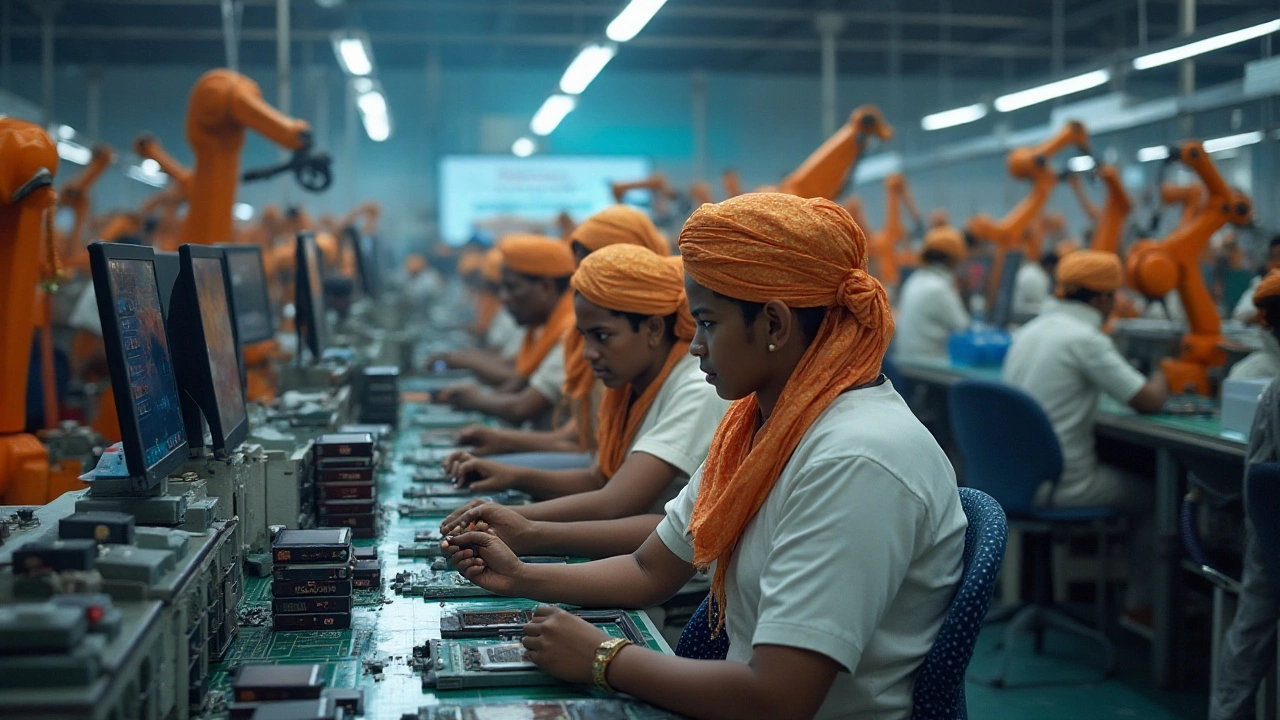
For centuries, manufacturing has powered economies, providing jobs and fostering innovation. Yet, today it finds itself under intense pressure. As modern technology evolves, the traditional model of manufacturing sees itself battling obsolescence.
Countries worldwide have experimented with varying government schemes to arrest and perhaps reverse the sector's decline. But as jobs continue to dwindle and factories close, one must ask: are these measures enough?
This article delves into the historical significance of manufacturing, the challenges it faces, the role of automation, and the impact of government interventions. We will also explore some potential strategies that might just reignite the once-thriving heart of industry.
- Historical Context of Manufacturing
- Current Challenges and Trends
- Government Initiatives and Their Effectiveness
- Technological Advancements and Automation
- Impact on Employment and Economy
- Strategies for Revitalization
Historical Context of Manufacturing
The history of manufacturing is a tale of evolution, innovation, and resilience. If we take a stroll down the cobblestone paths of history, we see manufacturing as a backbone that transformed small workshops into the bustling industrial complexes of the modern era. Initially centered around simple crafts and tools, manufacturing took a giant leap during the Industrial Revolution in the late 18th century. Steam engines roared to life, revolutionizing industries with newfound power and efficiency. This transformation not only bolstered economies but also seeded a societal shift from agrarian roots to an urban existence. As cities rose, so did the demand for goods, and manufacturing answered with mass production models, fueled by mechanization and assembly lines.
This period of unprecedented growth laid the foundation for what many would refer to as the golden age of manufacturing. The early to mid-20th century saw manufacturing reach its zenith, especially after World War II. It wasn't just about producing goods; it was about defining cultures and shaping national identities. Countries like the United States, Germany, and Japan became synonymous with manufacturing excellence, their names etched into history by the quality and innovation they consistently provided. The impact of Marshall plans, recovery strategies and trade agreements can't be understated for boosting industrial capabilities and economic prowess.
"Manufacturing, over the centuries, has been more than a sector—it's a reflection of human capability and vision," says historian Dwight Anderson. Such sentiment resonates as we recognize manufacturing's role in driving technological advances, promoting employment, and elevating standards of living across the globe.
Yet, as we approach the latter half of the 20th century and enter the 21st, signs of trouble stir. The emergence of globalization shifted manufacturing bases to regions offering cheaper labor costs. Countries in Southeast Asia, like China and Vietnam, capitalized on this, eroding the once-dominant position held by western nations. Outsourcing became a buzzword, emphasizing cost over domestic manufacturing pride. As economies continued to grapple with these shifts, the meaning and method of manufacturing began to change. Even technology, which once propelled manufacturing to great heights, presented challenges in the form of automation and digital processes. This story of adaptation is ongoing, a testament to both the enduring significance and current vulnerabilities of the industry.
Current Challenges and Trends
The manufacturing decline is a complex puzzle, woven with a variety of factors. Shifts in global economics, an ever-increasing pace of technological change, and evolving consumer demands all contribute. Today’s manufacturers are not just competing within their own borders; they vie on a global stage, battling against countries with cheaper labor and less restrictive regulations. According to a report by the World Economic Forum, “the global manufacturing landscape is changing and companies must adapt to survive.” This seeping transformation has left many industries vulnerable, pining for the golden days of robust production levels.
One significant pressure point is cost management. Industries face rising costs on multiple fronts – from raw materials to logistics. Couple this with razor-thin profit margins, and the situation becomes even more precarious. As companies struggle to remain globally competitive, they often seek ways to reduce costs. This includes outsourcing jobs to nations with a more favorable economic climate. This practice, though financially appealing in the short-term, creates longer-term issues, such as job loss and skill erosion in domestic markets.
Another major issue is the swift pace of technological change. Today, industries are expected to evolve rapidly with the times, embracing advancements to remain relevant. Automation and robotics, for example, though crucial for efficiency, have displaced jobs traditionally held by human workers. This shift has resulted in a skills gap – where available workers do not meet the advanced skill set requirements of modern manufacturing roles. A survey from Deloitte highlighted that despite the decline, there are still millions of unfilled manufacturing jobs due to this skills mismatch.
Moreover, consumer behavior is influencing manufacturing trends more than ever. Modern consumers prioritize sustainability, demanding products that are not only high-quality but also environmentally friendly. Manufacturers must now contend with producing goods that adhere to green standards, all while managing their bottom line. Companies like Tesla have managed to thrive by aligning their products with these consumer values, but for many traditional manufacturers, such adaptation poses significant financial and operational challenges.
Finally, geopolitical tensions have also impacted the industry landscape. Trade wars and political sanctions can disrupt supply chains and increase uncertainty in production planning. Manufacturers must navigate tariffs and import/export restrictions, all while maintaining product quality and pricing structures. It’s a delicate balancing act, akin to walking a tightrope with a shifting base.
“Manufacturing today is on the brink of a revolution. Those who adapt will thrive, those who resist will perish,” remarked a renowned economist. The call for adaptation isn’t just a buzzword; it’s a vital strategy for survival in this ever-shifting industrial terrain.
All these challenges and trends showcase a need for strategic innovation and agile adaptation. Not just to survive, but to thrive, manufacturers must be ready to ride the winds of change with dynamic responses. As we delve further into government initiatives in other sections, it becomes evident how these challenges are being addressed differently across the globe.
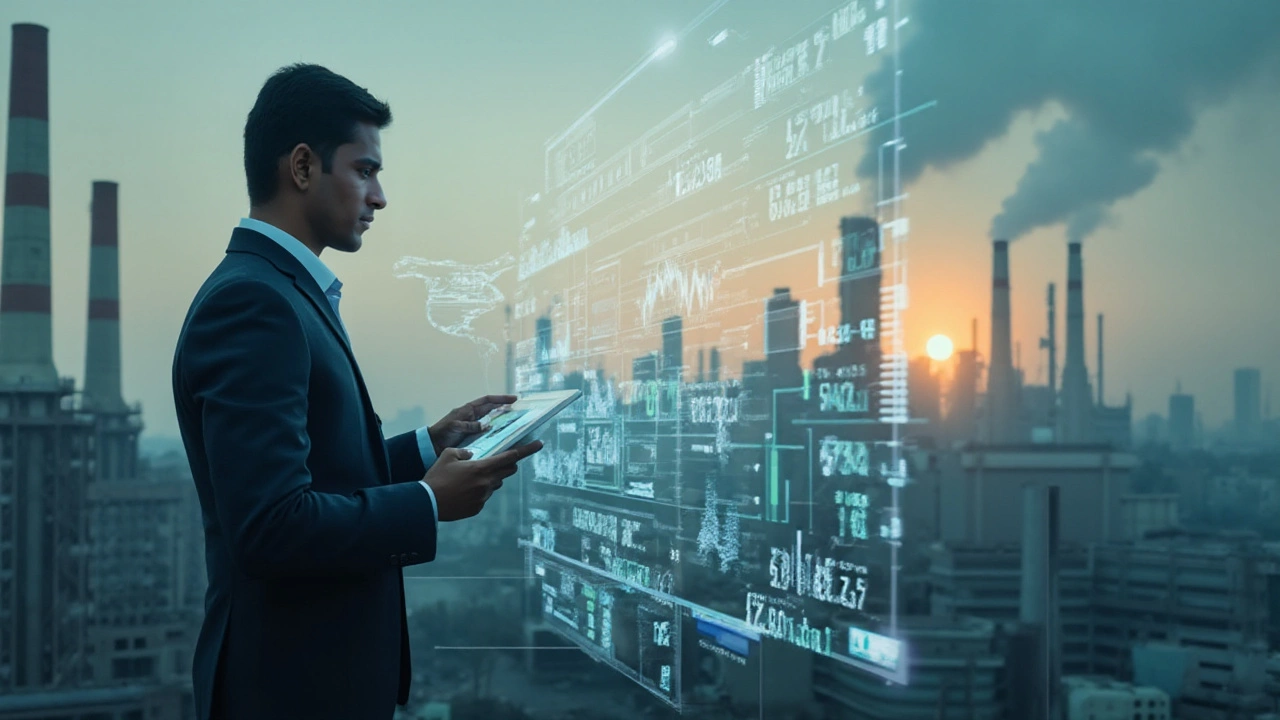
Government Initiatives and Their Effectiveness
Governments worldwide have long recognized the pivotal role of the manufacturing industry in economic development. In an effort to address the sector’s challenges and buffered by evolving global dynamics, they have rolled out a tapestry of initiatives. These range from financial incentives, subsidies, and tax breaks to extensive research grants aimed at driving innovation. Notable schemes include America’s 'Manufacturing USA' institutes which foster public-private partnerships to accelerate technological advancements. Similarly, in Europe, the 'Industry 4.0' framework has been instrumental in steering traditional manufacturing toward digital transformation. While these plans are ambitious, their efficacy remains under scrutiny.
For instance, among the scores of policies enacted, the effectiveness of targeted tax incentives often sparks debate. While they provide short-term relief to manufacturers, critics argue that they can inadvertently benefit larger corporations at the expense of smaller, local businesses. Such disparities highlight the complex nature of designing comprehensive policies that cater to an increasingly fragmented market. The same goes for direct subsidies. While they promise to stabilize ailing sectors, their long-term impact can be uncertain, raising questions about economic efficiency and resource allocation.
Industry challenges also include securing skilled labor. In response, governments have infused substantial investments into vocational training and reskilling programs. Germany's dual education system stands out as a prime example, combining apprenticeships with classroom learning to create a workforce adept at modern manufacturing practices. Yet, such systems require substantial time and cultural adaptability to implement globally.
Equally critical to the discourse are public-private partnerships which seek to bridge innovation gaps. When governments ally with private entities, they not only inject capital but also enhance knowledge transfer. This model fosters cutting-edge developments in high-priority sectors, paving the way for scalable and sustainable manufacturing solutions. However, these partnerships are not without their challenges. Potential conflicts of interest and navigating regulatory landscapes can stall or complicate progress.
"Effective governmental initiatives in manufacturing demand not only strategic vision but an unparalleled commitment to adaptability and collaboration," an industry expert once remarked.
Balancing short-term gains with long-term resilience is central to any successful government initiative. With the global shift towards sustainability, governments must ensure policies align with environmental commitments. These measures must promote cleaner, greener manufacturing processes. Recent reports suggest that solar and wind industries have been major beneficiaries of such green-focused initiatives.
The question that lingers is how these government schemes in manufacturing measure against their intended goals. Are they robust enough to catalyze an industry-wide revival, or do they merely serve as sticking plasters? Continuous evaluation and iterative policy design are imperative. The journey of revitalizing manufacturing is undoubtedly intricate, yet with the right blend of innovation, policy, and collaboration, a renaissance is within reach.
Technological Advancements and Automation
The landscape of manufacturing is undergoing a seismic shift, driven largely by technological advancements and the rapid incorporation of automation. This evolution is not just a gradual change but represents a transformative phase that challenges traditional manufacturing methods. Automation in particular, led by robotics and AI, promises increased efficiency and precision, yet it simultaneously raises profound questions about the future of the workforce. Robots are no longer confined to repetitive tasks; they are now undertaking roles that require cognitive abilities, previously the domain of skilled workers. This progress, while remarkable, creates a precarious balance between innovation and employment.
Interestingly, the introduction of next-gen technologies like 3D printing and the Industrial Internet of Things (IIoT) has revolutionized production capabilities. These technologies allow manufacturers to design and produce complex parts with minimal lead time and waste. IIoT connects machines and systems, enabling real-time data exchange, which can improve predictive maintenance and product quality. Yet, these advancements come with their own set of challenges. Manufacturers must navigate cybersecurity threats while integrating these technologies, as these sophisticated systems can become attractive targets for cyber-attacks if not properly secured.
Shift in Workforce Dynamics
Automation has distinctly altered labor dynamics as well. The demand for traditional assembly line workers has decreased, while there is a rising need for employees skilled in tech and data analysis. This shift necessitates robust re-skilling initiatives. A report by McKinsey suggests that nearly 14% of the global workforce may need to switch job categories by 2030 in response to automation-driven disruptions. There lies a great opportunity for government schemes and educational institutes to bridge the skill gap by tailoring programs that equip workers with the necessary digital competencies. As the manufacturing decline persists, re-skilling becomes a crucial strategy for both workers and businesses looking to remain competitive.
Amid these developments, it's important to note that not all is destined to go digital. A nuanced understanding of when and where to apply these technologies is critical. Noted economist and expert Charles Duhigg once said,
"The key to future-proofing manufacturing is not just about adopting new technologies, but understanding how they integrate with human workers to create value."This aligns seamlessly with the trend of 'co-bots', or collaborative robots, that are designed to work alongside humans, enhancing rather than replacing human effort.
The impact of technological advancements in manufacturing is multifold. While it's compelling to pursue heightened productivity through automation, the economic impact of displaced jobs cannot be dismissed. Policymakers are increasingly looking at how to craft and implement comprehensive government schemes to cushion the blow for workers and industries alike, ensuring a balanced approach to modernization in the manufacturing sector. These efforts will play a key role in determining whether the industry can adapt effectively to embrace these technological changes.
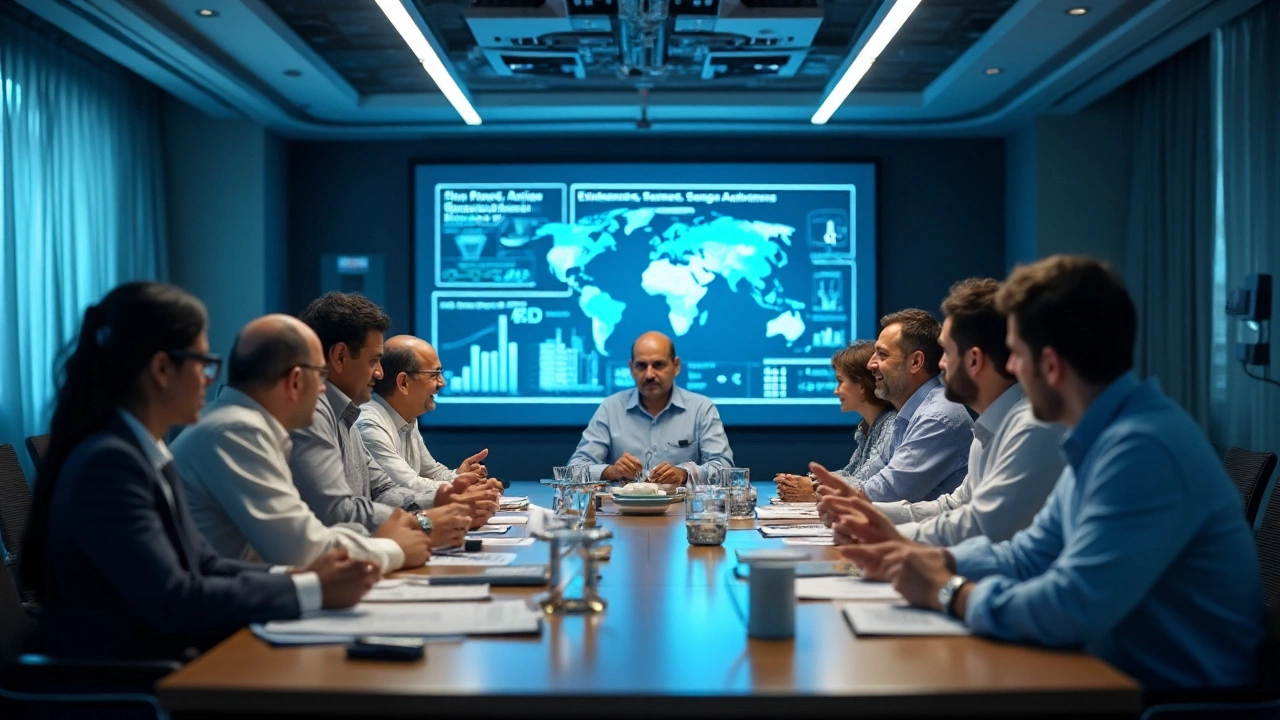
Impact on Employment and Economy
The decline of the manufacturing industry is casting a long shadow over employment landscapes worldwide. Traditionally, manufacturing has provided stable and well-paying jobs for millions of workers. As industries adapt to technological advancements and automation, the employment structure is rapidly transforming. Modern manufacturing relies heavily on technology, reducing the need for manual labor. This shift has left thousands searching for new livelihoods, disrupting families and communities along the way.
The impact of this shift is starkly visible in regions historically dependent on manufacturing plants. Cities and towns that thrived during the industrial boom now face economic stagnation. Unemployment rates in these areas soar, making job recovery a challenging quest. The transition to a tech-driven model doesn't just cut jobs; it creates an economic ripple effect. Local businesses suffer when fewer workers are able to support them, which then further fuels the economic downturn.
Interestingly, despite the decline in traditional roles, opportunities in tech-centric manufacturing are on the rise. Yet, the skill gap is a formidable barrier. Industries are in dire need of workers proficient in operating sophisticated machinery, and there's a push for retraining programs. But moving workers from the assembly line to the control room isn't straightforward. It requires comprehensive restructuring of workforce education and a mindset shift among workers and employers alike.
There's also an impact on the broader economy. Manufacturing sectors significantly contribute to GDP in many countries. Their decline has forced governments to reconsider economic strategies. The rise of service sectors offers some compensation; however, these industries rarely provide similar levels of economic output. Efforts to stimulate these economies include tax incentives, monetary support for innovation, and trade agreements.
"The solution might not be to save all old jobs but to create pathways towards the jobs of tomorrow," suggests renowned economist Dr. Aisha Patel.
Let's not forget the challenges of transitioning economies that rely heavily on exports of manufactured goods. Currency valuations, trade tariffs, and international competitiveness play heavily into how these industries evolve. In an increasingly interconnected world, the shifts in manufacturing have repercussions far beyond individual borders. The balance of global trade depends significantly on the health of this sector.
As the manufacturing decline continues to evolve, it becomes ever more crucial for policymakers to rethink and reprise their strategies. Creating sustainable economic models that balance technological prowess with human capital development will pave the way forward. Whether this means fostering innovation hubs, reforming education systems, or incentivizing advanced manufacturing techniques, the focus must remain on creating a robust, adaptive economy that serves all.
Strategies for Revitalization
When it comes to breathing new life into the manufacturing sector, there's no magic formula, but certain strategies can provide a meaningful impact. One approach centers on investing in state-of-the-art technology. This includes the integration of artificial intelligence and the Internet of Things (IoT) into the manufacturing processes. By embracing such advancements, manufacturers can enhance efficiency, reduce waste, and tailor production to meet emerging consumer demands. The shift towards smart factories is a game changer that could redefine the future of the sector.
The importance of workforce development cannot be overstated. As technology continues to evolve, so too must the skills of the employees. This means that governments and educational institutions need to collaborate closely to ensure that curricula are updated and relevant. By focusing on upskilling and reskilling programs, workers can be better equipped to handle new technologies and methodologies in production. An industry expert once remarked, "Investing in human capital is as crucial as investing in technology itself." This insight underscores the dual focus needed to propel manufacturing into a new era.
Another vital strategy involves enhancing global competitiveness. Domestic manufacturing must not only aim to produce superior products but must also become more economically viable in the international market. This can be achieved through strategic partnerships and by reinforcing supply chains. A resilient supply chain can lessen the impact of global disruptions, ensuring that domestic industries remain robust in fluctuating markets. Governments can play a role by fostering trade agreements that benefit the manufacturing sector and by offering incentives for expanding export capacities.
Sustainability is not just a buzzword; it's a crucial component of modern manufacturing strategies. By adopting greener practices and reducing carbon footprints, manufacturers can not only appeal to environmentally conscious consumers but also comply with increasingly stringent regulations. This involves a holistic review of production processes, from sourcing raw materials sustainably to implementing energy-efficient technologies. Data from recent studies reveals that companies who prioritize sustainability often see improvements in brand reputation and customer loyalty, leading to long-term operational success.
There are some who advocate for policy reform as a means of reinvigorating manufacturing. Governments could reassess taxation and regulatory frameworks to create a more conducive environment for industrial growth. Tailored policies that support startups and innovation within the sector can lead to increased investment and job creation. By making it easier for small and medium enterprises (SMEs) to thrive, the manufacturing landscape can become more dynamic and diverse.
The specific combination and emphasis of these strategies can vary greatly depending on regional strengths and weaknesses in industrial challenges. Those in leadership positions must weigh their options carefully to align their strategies with local economic realities and global trends. In essence, the path to revitalizing manufacturing is multifaceted and requires the joint effort of governments, industries, and communities to unlock new possibilities for growth and sustainability.